Information
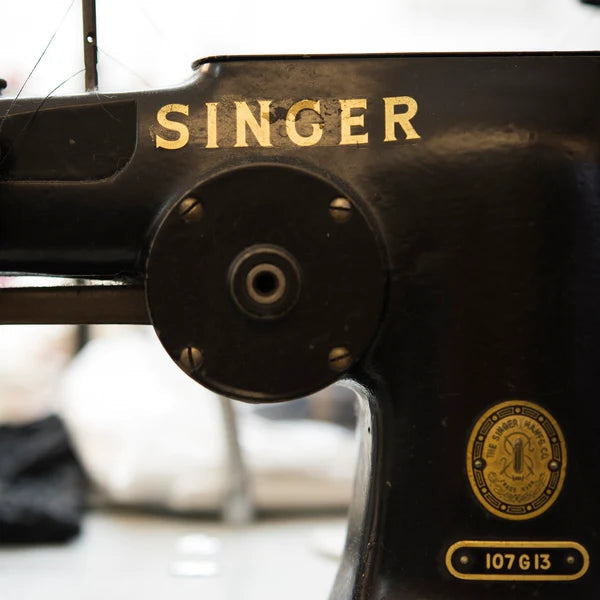
Our glovemaking
The hub of our glovemaking operation is a small, flint walled building that was built some 150 years ago to house dairy cows. All around us are pastures. A mile to the south, the green hills of th...
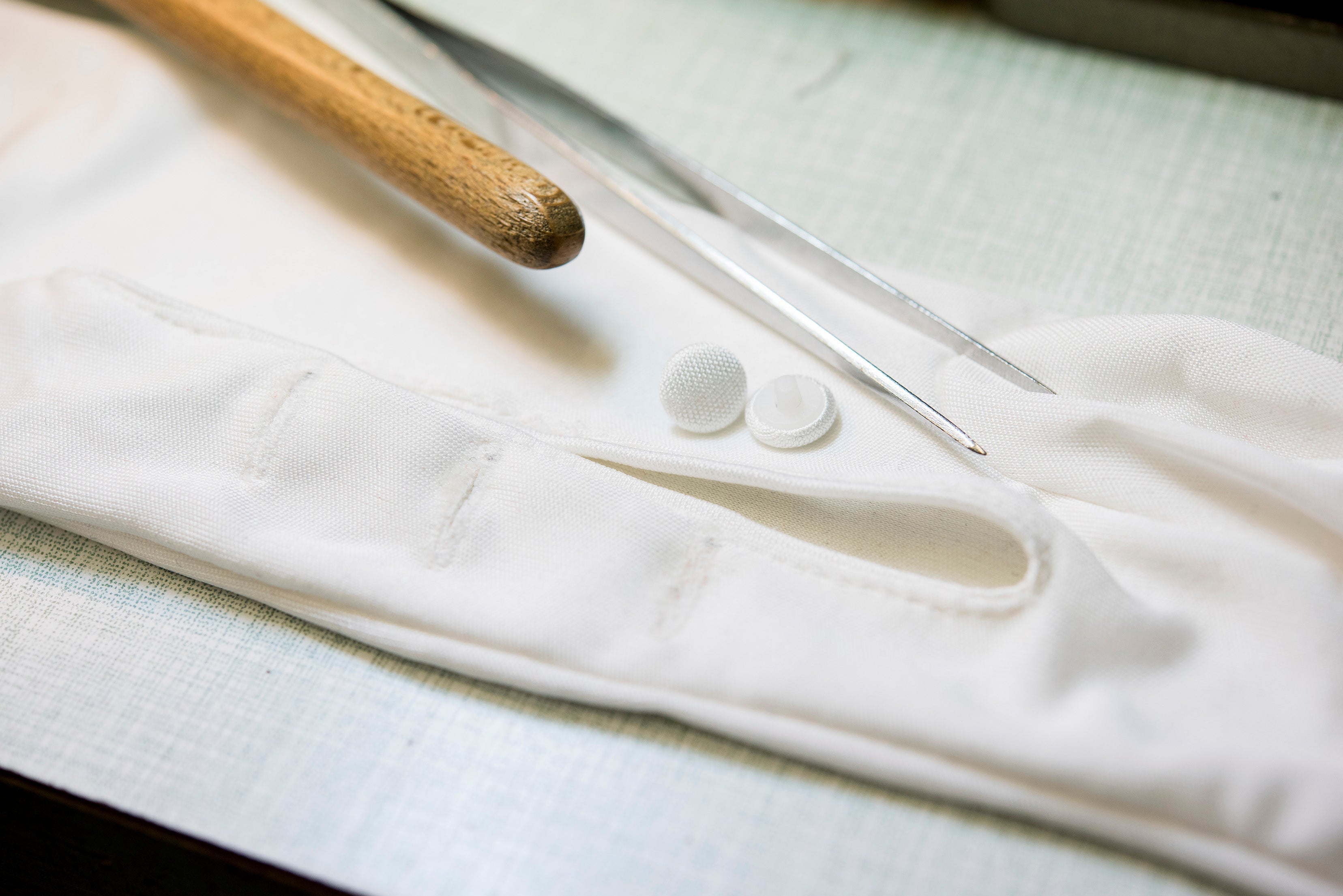
Glove length | Button length
The length of a glove up the wrist and arm is traditionally measured not from the fingertips but from the thumb seam at the base of the thumb. The traditional unit of measurement is a 'bouton' or,...
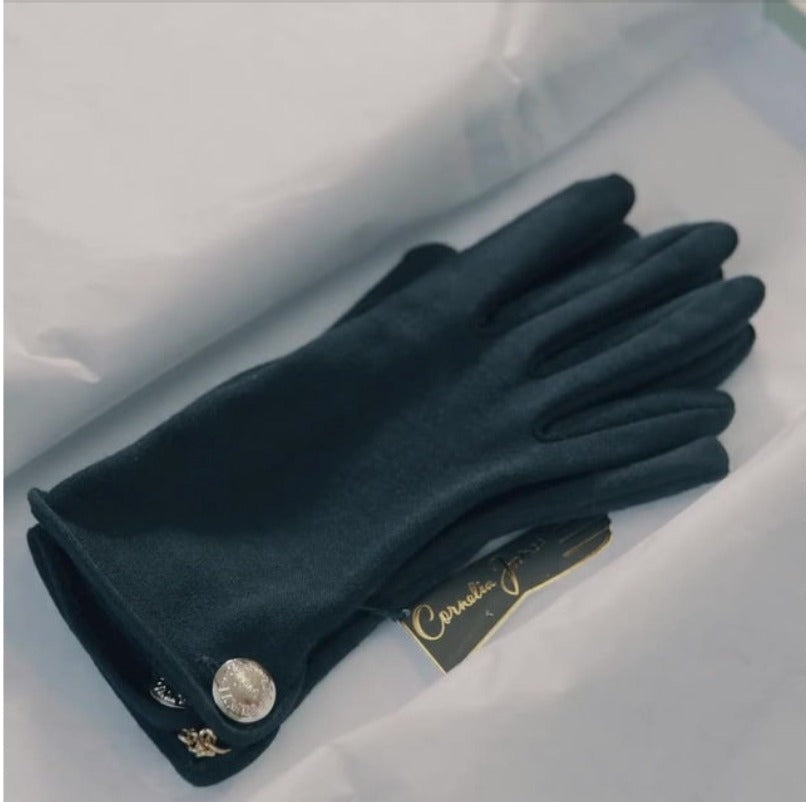
Our glovemaking
Are we doing it wrong? All over the world there are factories churning out gloves by the container load. Here, at Cornelia James, it’s not quite like that. We do like to think of ourselves as havin...
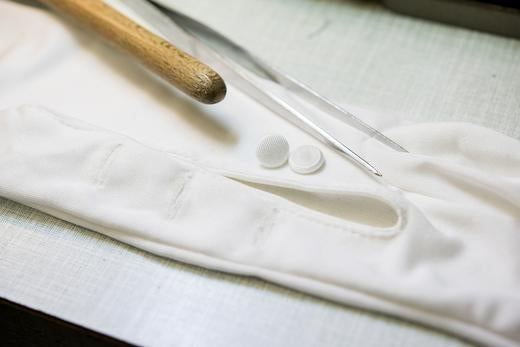
The mousquetaire opening
The mousquetaire is a feature which can be added to a long evening glove. It is an opening on the inside of the wrist fastened by three little buttons which allow you to remove your hand from the ...
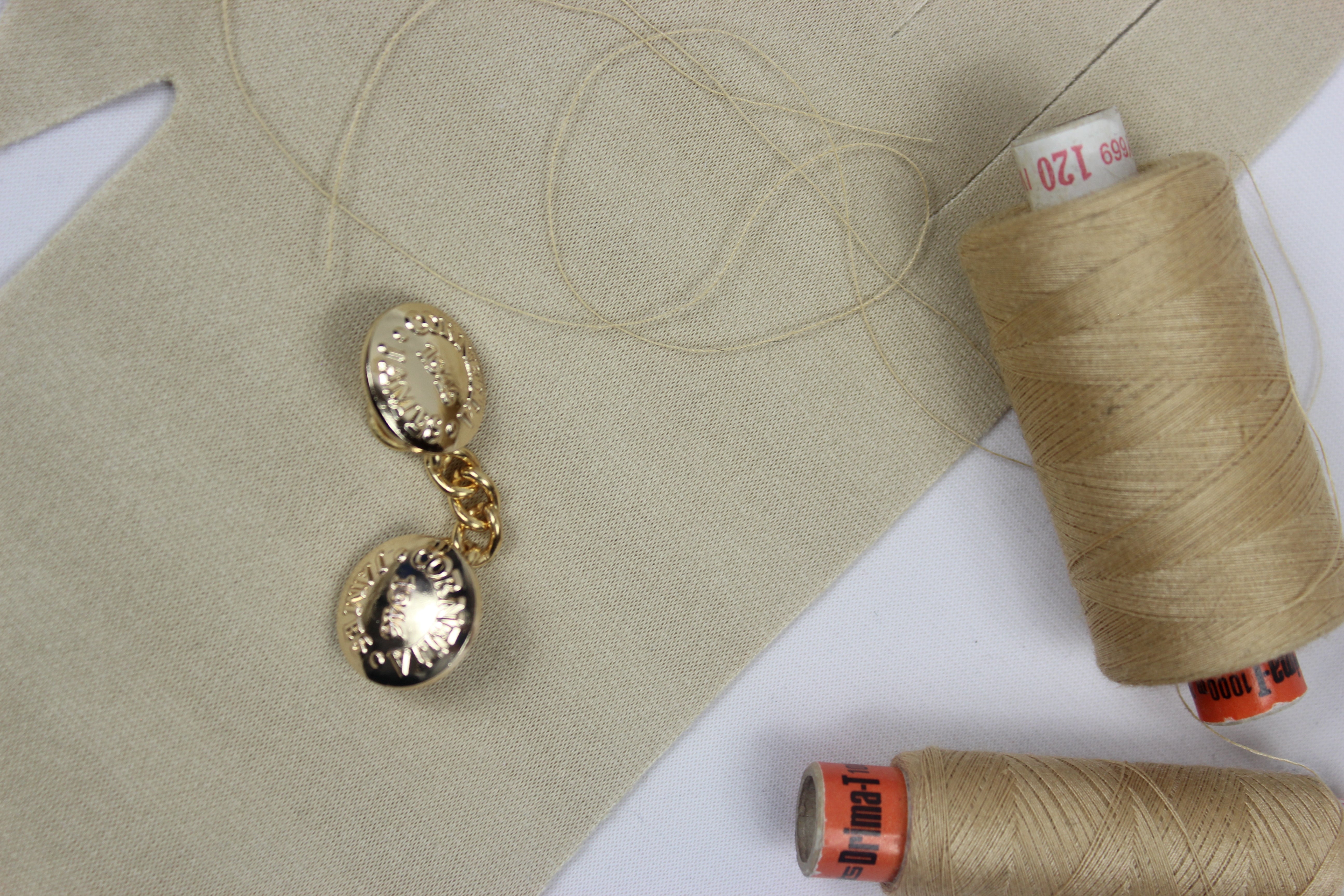
How they’re made: Sueded Cotton gloves - Georgina
At a time where fast fashion and mass production seem to be the easy option for both the company and the consumer, we take pride in knowing that each pair of our gloves is made by one of our glove...
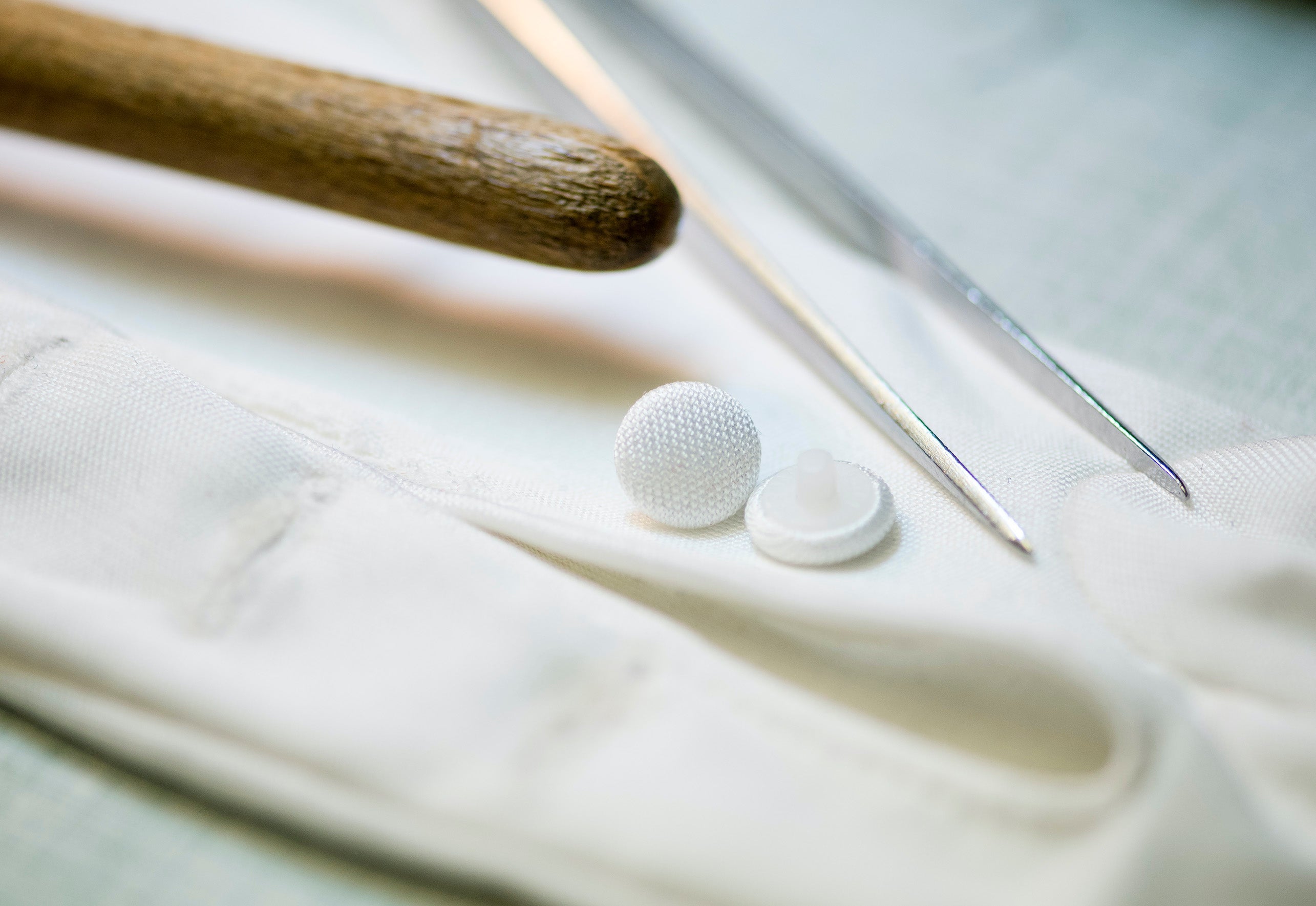
Bespoke gloves
Can you do bespoke colours?
If you are looking for a precise colour match, some of our fabrics dye really well. In particular the Pure Silk and Duchess Satin are really excellent for dyeing. All w...
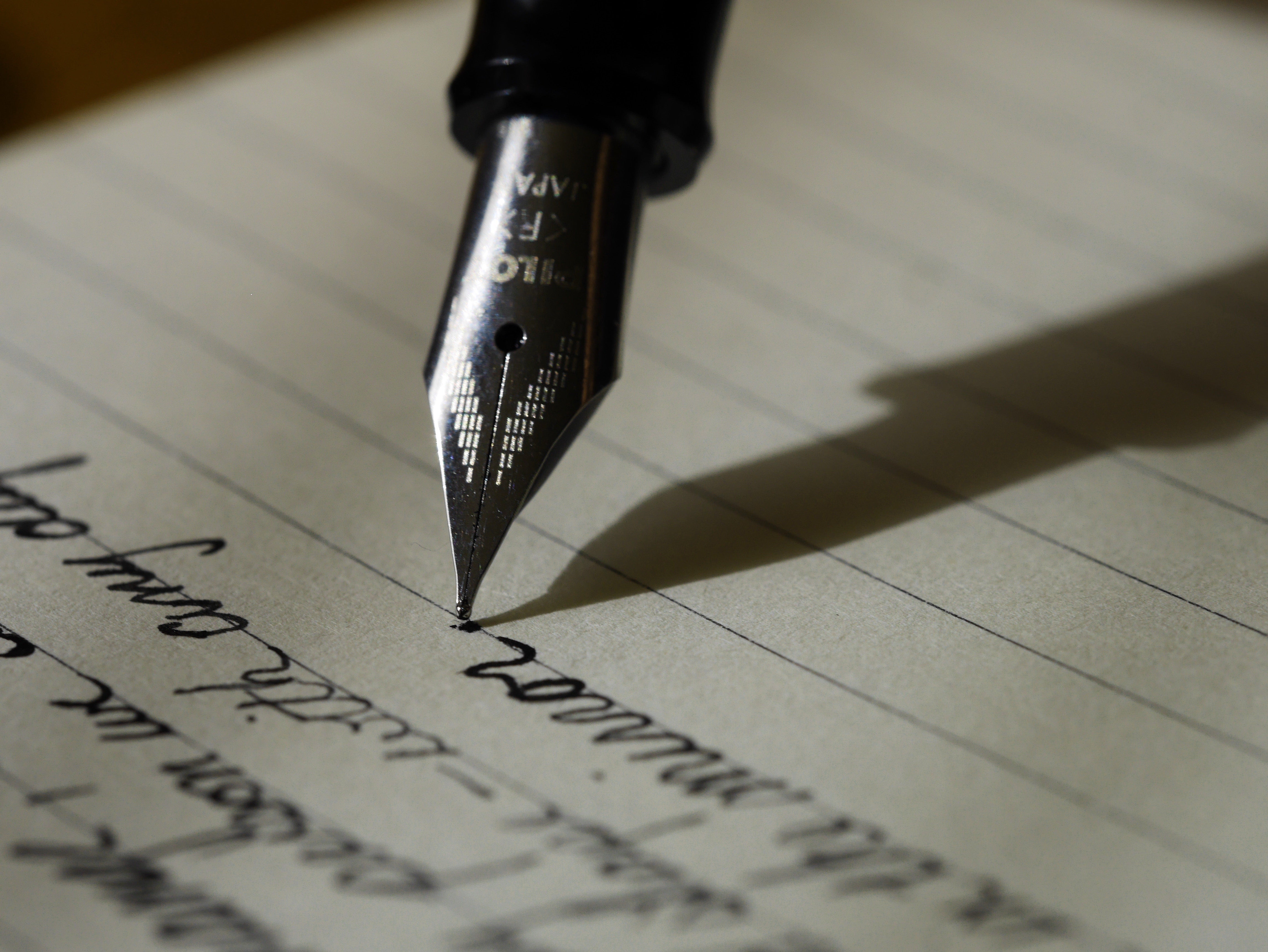
Our history
"Design student flees Nazi scourge, arrives in England with suitcase full of fabrics, finds fame and fortune as glove maker to the Queen"
It is the stuff of legends and 70 years on the fashion b...
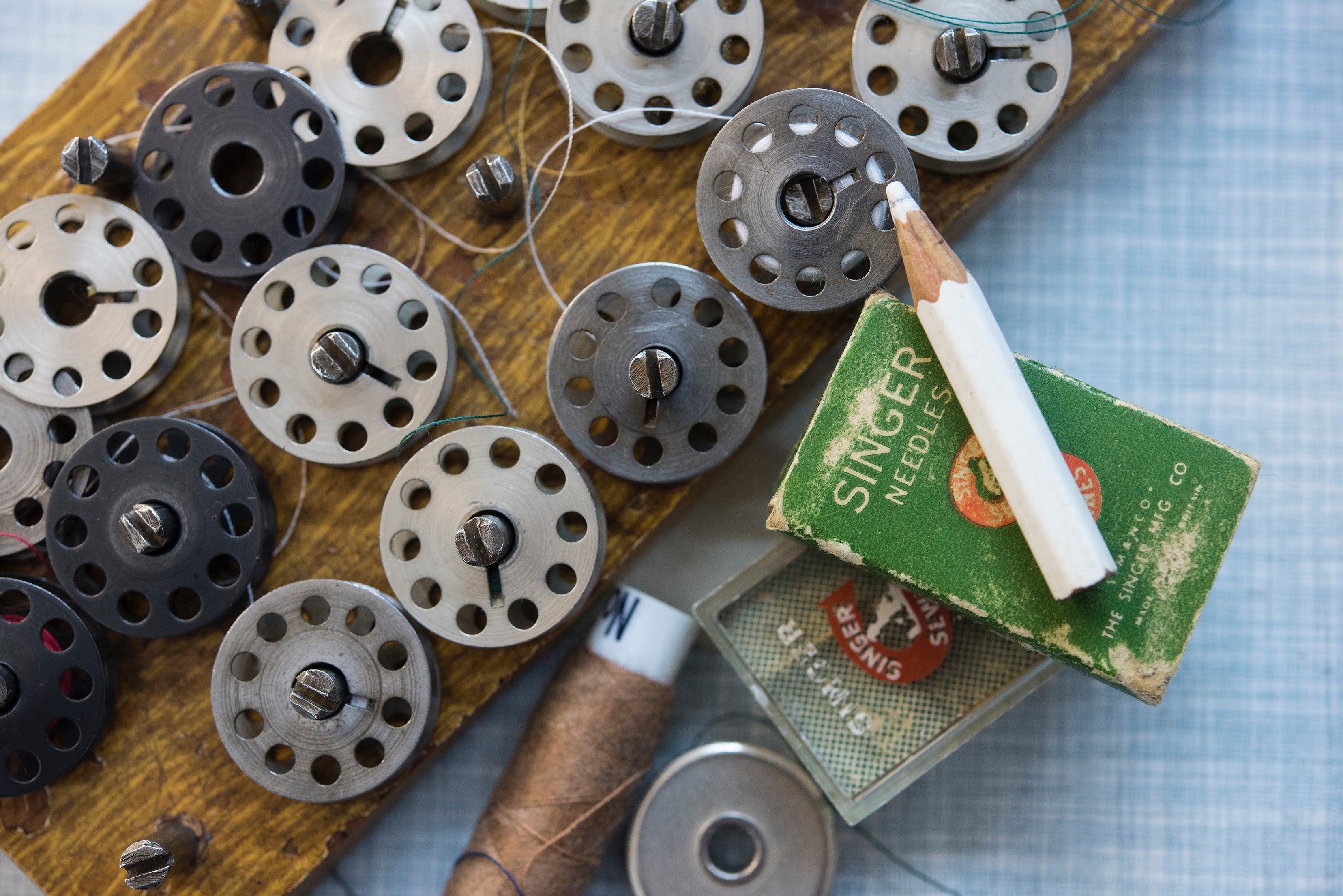
Our story
We are glove makers. That is really all we do. But we try to do it really well and we have been doing it for a long time. We do it because we think that gloves are important and because a good pair...
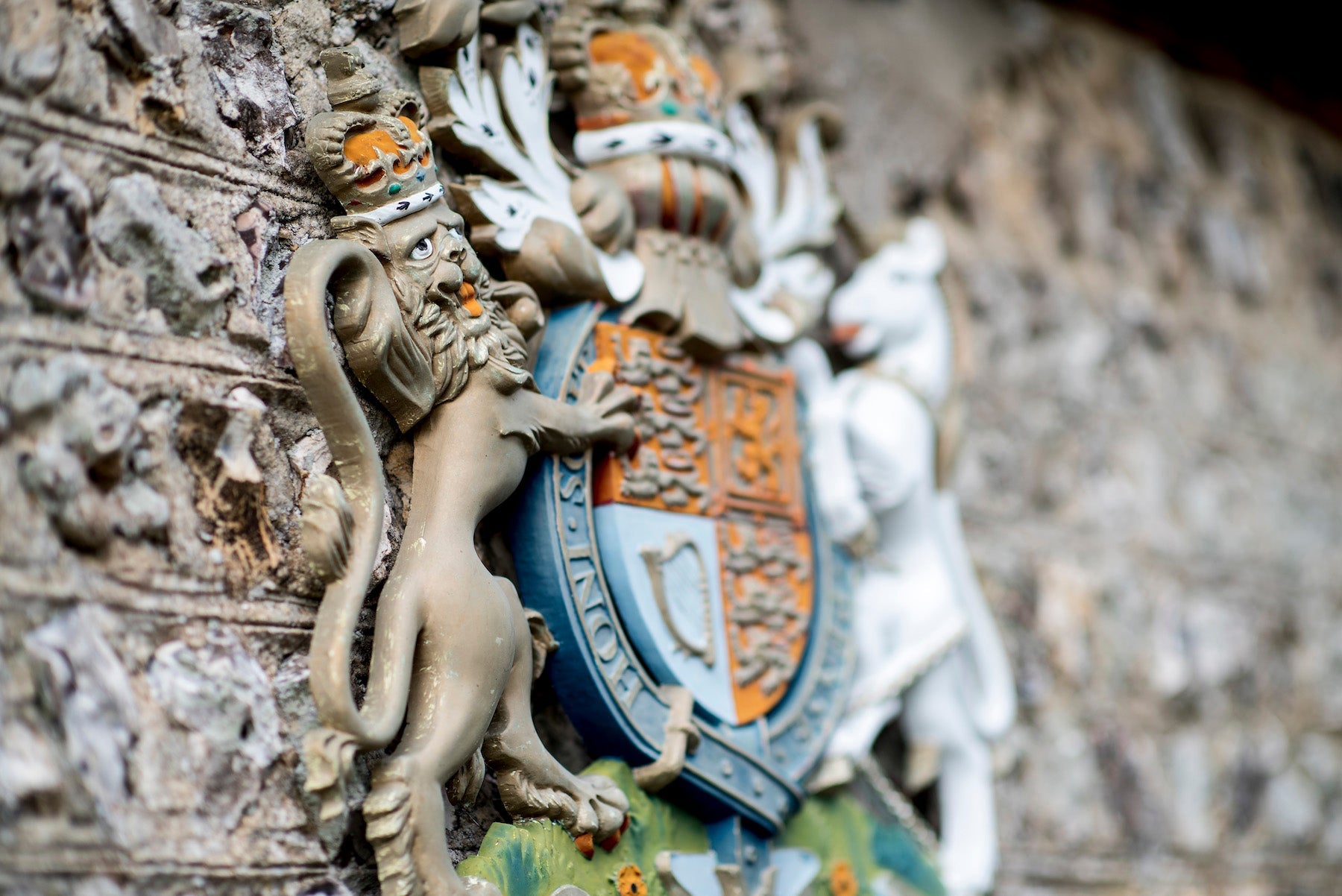
Royal Warrant | 1979
We are glove manufacturers by appointment to Her Majesty the Queen. Our association with the Queen goes back to 1947 when Norman Hartnell, who had been asked to make the young Princess' going away...